This last week I learned a rather interesting lesson about quality and systems thinking. To set the context:
End of June I bought myself a new bicycle for the first time in 20 years, a road/race bike. When looking for potential models I focused on one set of components (brakes, groupsets and all that). Regarding frame and wheel set I had no preference. Buying a bike in 2021 is anyway a rather hopeless endeavor. I was very lucky, when I found a shop in Ingolstadt (about 85km away) that had one in my frame size in stock.
When riding through the “outback” last week, I hit one bump and heard a crack. A spoke broke and my tour that day was done. I called my wife to pick me up.
As someone with an aspiration to be a maker, I wanted to fix it myself. I had done it before (truing more often, replacing a spoke ages ago, but okay), so why not this high-tech thingy of a wheel. While waiting, I was searching on my mobile for replacement parts. There actually was a maintenance set by Newmen with a set of spokes, nipples and washers on the market. Only problem, it was sold out in all shops that I could find.
To save me some time – how funny that sentence is, only came to my realization 7 days later – I decided to bring the wheel to one of the bike repair shops in the vicinity. On Saturday I tried one in my town, who also sells race bikes. They didn’t have the right length of spokes in stock and were about to go on vacation. The one in the next town didn’t have one exactly the size, but wanted to try it. On Tuesday he called me, that it didn’t work. Ordering replacement parts was not in his interest, as he has to order them by the 100. I called a few more bike shops, but no success.
So I started looking again on the internet. I found the right length of spokes (as pack of 20), and got offered also the right tools I needed under “What other customers were also buying”. 3 days later the parcel arrived, exactly 1 week after the incident. I took the Friday afternoon off to fix the wheel.
I removed the rim tape, was able to shake out the nipple with the broken spoke threading, and put the wheel on the truing stand. I checked the packs of spokes, and the longer ones seemed to be the right ones. Only the nipples looked different. The ones that came with the new spokes had a slit on the side where they should hit the rim. That slit fitted to one of the fancy special tools that I ordered. But that way around the tool was useless. So I checked the spoke wrench. That one didn’t fit as well. WTF? Never blindly trust an algorithm!
I was grumpy – for a change – took one nipple as example and drove to a couple of bike shops (5!) to find a fitting spoke wrench. I haven’t seen so many confused faces in a while. One was even mansplaining me, that I am wrong, and that’s not the way these things are supposed to work, and the tool I’m looking for doesn’t even exist. At the last shop on that round I had a nice chat with the boss, chatting about shortage of materials on the market and other things. Also he didn’t know about that way of mounting nipples. But he gave me the tip to call the manufacturer.
On my way home, already driving around through the county for over 90 minutes, I decided to call the shop in Ingolstadt first. Luckily the guy picked up the phone who had sold me the bike. A true bike freak. I told him my problem and he immediately understood and told me that the wheel set had to be sent to the manufacturer. I should come by and they would arrange a replacement wheel set, until mine is coming back from the manufacturer. So, back into the car, driving 1h north to Ingolstadt, and finally all pieces of the puzzle came together.
Someone had an idea
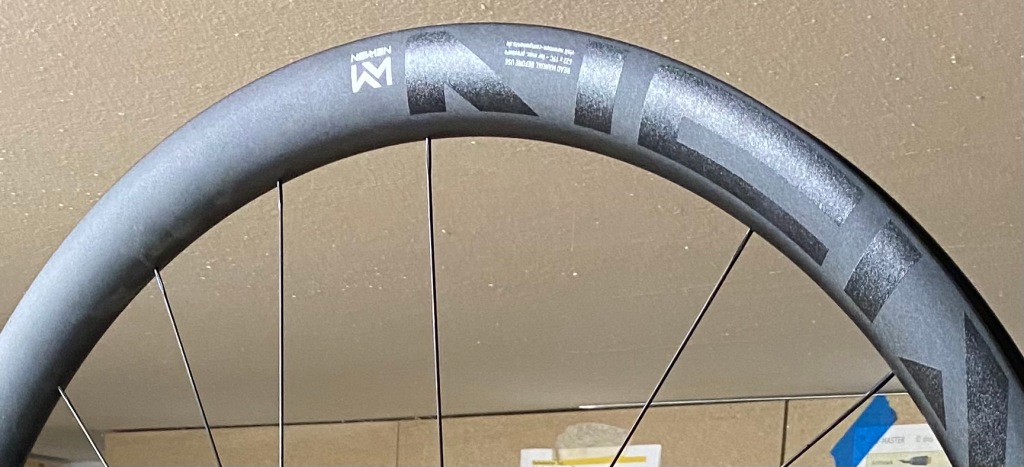
Someone at Newmen had a fancy idea. To achieve a cleaner look on the rims, they basically turned the nipples around to fix the spokes from inside the rim.
Here is a rough sketch to illustrate the idea. Newmen produced nipples with a clean head (no slit) to prevent shaving off the rim, when screwing the spoke in. To do that, you need a long tool with a slim head and a 3mm square profile to reach the nipples inside the hollow chamber of the rim (an inside nipple wrench). Also the holes on the rims are much smaller, as only a 2mm spoke has to fit through it. Nice idea!
Basically the Rest of the World (ROW) is doing it differently. They drill a bigger hole in the rim, and fiddle the nipple through that hole. The nipple with its square profile is then outside of the rim and reachable by the standard nipple wrenches. That also explained the slit on the nipples I received and the special tool to fiddle them in.
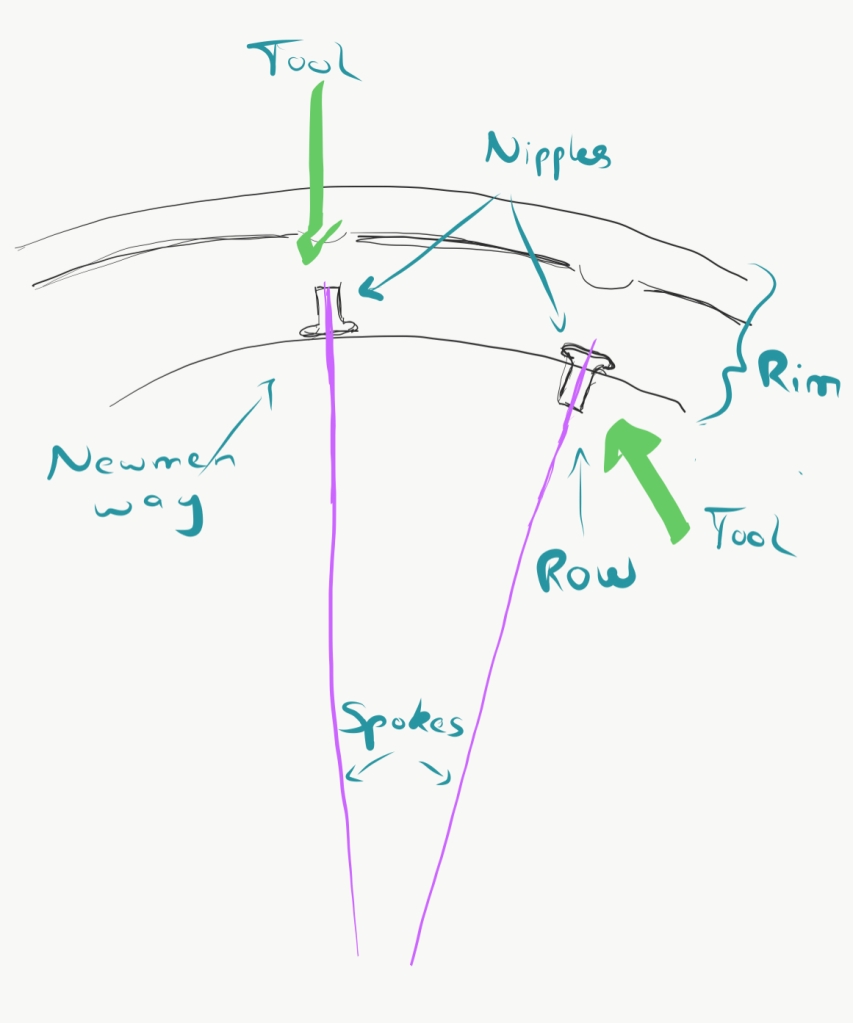
And this design change explained everything I have experienced the past week. The stunned faces, the material shortage, the inability to find someone able to help me.
The Balance of Quality Criteria
What the manufacturer did was underestimating the right balance between two quality criteria. The two competing aspects in this case were “Look/Attractiveness” and “Maintainability”.
Yes, hiding the nipples inside the rim created a cleaner, crisper look.
BUT! That means trouble for maintenance. And here systems thinking comes into the picture. When you look at one thing to improve its quality, you have to keep the environment/system that it is running in, in mind. In case of Newmen, they forgot the bike repair shops and people maintaining their bikes themselves.
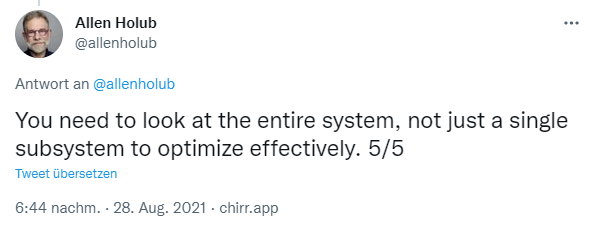
Because not only to change entire spokes, but also to simply true a wheel, you need to remove the tires, tubes, and rim tape. Truing a wheel, mounted on the bike, is basically impossible that way. And you need special tools, that many shops don’t even know about (5 out of 6 in my vicinity). And also special spare parts, as the nipples need to be without a slit.
In manufacturing this is probably not too much of a change, as you have a naked rim on a truing stand in front of you, and where from to apply the tool to change the tension of the spokes is just a matter of exercise and training.
As long as the wheel is intact and functioning 100%, all is fine. But as soon as you face an issue, all that beauty is getting in the way of quality!
Newmen has accepted that fact and will most probably / hopefully now redrill my rims and re-equip them with standard nipples, ones that look out of the rim. I was told by the bike salesman, that they had seen the problems happening quite fast, once the wheels were out in the field and changed their design mid-year of production, which rarely happens in the bicycle industry.
As a side note, I also don’t expect that the maintenance set for that rim to get back in stock.
When I buy my next bike, I know now one more quality aspect to look for. But now I wait for my wheel set to return in a few weeks.
One thought on “A Lesson about Quality Balance and Systems Thinking or “Zen and the Art of Bicycle Maintenance””